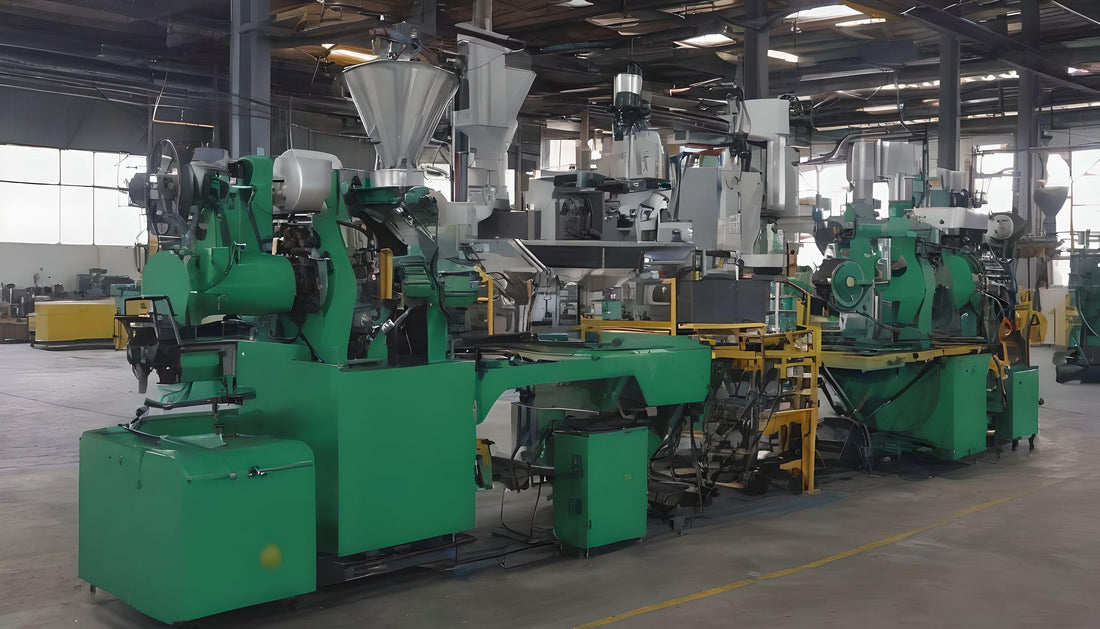
What is CCA Copper Clad Aluminum Wire?
Share
Introduction
Copper Clad Aluminum wire (CCA) is a type of electrical wire that features an aluminum core coated with a thin layer of copper. This wire combines the excellent conductivity properties of copper with the lightweight and cost-effective benefits of aluminum. Copper Clad Aluminum wires (CCA) are widely used in various industries, including telecommunications, electrical installations, and automotive applications.

What are the Components of CCA Wire?
Core Material: Aluminum
Aluminum is chosen as the core material for Copper Clad Aluminum wire due to its numerous advantageous properties. Here are some key characteristics of aluminum:
- Lightweight: Aluminum is significantly lighter than copper, making it easier to handle and install, especially in large-scale applications.
- Abundant and Cost-Effective: Aluminum is more abundant in the Earth's crust compared to copper, making it a more cost-effective option.
- Corrosion Resistance: Aluminum naturally forms a protective oxide layer, providing resistance to corrosion.
However, using aluminum as a core material also has some drawbacks:
- Lower Conductivity: Aluminum has lower electrical conductivity compared to copper.
- Brittleness: Aluminum is more prone to breaking under tension or repeated flexing.
Cladding Material: Copper
Copper is utilized as the cladding material in Copper Clad Aluminum wire CCA for its superior electrical properties. Here are the main characteristics of copper:
- High Conductivity: Copper is known for its excellent electrical conductivity, which helps in transmitting electrical signals efficiently.
- Flexibility: Copper is more flexible and can withstand bending and twisting without breaking.
- Thermal Conductivity: Copper has high thermal conductivity, which is beneficial in applications where heat dissipation is crucial.
The copper cladding provides several benefits:
- Enhanced Conductivity: The copper layer significantly improves the overall electrical conductivity of the wire.
- Corrosion Protection: Copper cladding helps protect the aluminum core from oxidation and corrosion.
- Improved Mechanical Strength: The copper layer adds mechanical strength and flexibility to the wire.

Manufacturing Process
Step-by-Step Process
Step 1: Preparing the Aluminum Core
The manufacturing process of Copper Clad Aluminum wire begins with the selection and preparation of high-purity aluminum rods or wires. The chosen aluminum material undergoes rigorous cleaning and pre-treatment procedures to ensure its purity. These procedures remove any impurities or contaminants that could affect the final product's quality.
Step 2: Applying the Copper Cladding
The next step involves applying the copper cladding to the aluminum core. There are several methods for achieving this:
- Electroplating: In this method, the aluminum core is submerged in a copper electrolyte solution. An electric current is passed through the solution, causing copper ions to deposit onto the aluminum surface, forming a thin and even copper layer.
- Hot Dip Method: The aluminum core is dipped into molten copper, allowing the copper to bond to the aluminum surface. This method ensures a thick and durable copper coating.
- Welding Techniques: Copper can be welded onto the aluminum core using specialized welding processes, creating a strong bond between the two metals.
- Extrusion Process: The aluminum core is passed through a copper die, which physically presses the copper onto the aluminum surface, forming a cladded wire.
Step 3: Bonding Layers Together
After the copper cladding is applied, it is essential to ensure a uniform and durable bond between the copper and aluminum layers. This is achieved through various bonding techniques that enable the copper to adhere securely to the aluminum core. The goal is to create a seamless and strong bond that will withstand mechanical stress and electrical currents.
Step 4: Final Processing
The final step in the manufacturing of Copper Clad Aluminum wire CCA process, involves drawing the wire down to the desired gauge. This step ensures that the wire meets specific thickness and diameter requirements. For certain applications, the wire may undergo an annealing process to enhance its flexibility and make it easier to work with during installation.
Quality Control Measures
To maintain high standards, several quality control measures are implemented during the manufacturing of CCA Copper Clad Aluminum wire:
- Testing for Adhesion Strength: The bond between the copper and aluminum layers is tested to ensure it is strong and durable, preventing separation under stress.
- Electrical Conductivity Tests: Conductivity tests are conducted to verify that the wire meets the required electrical performance standards.
- Compliance with Industry Standards: CCA Copper Clad Aluminum wire is subjected to rigorous testing to ensure it complies with industry standards and regulations for safety and performance.
Advantages of CCA Copper Clad Aluminum Wire
CCA wire offers several advantages over pure copper wire, making it a popular choice in many applications. Some key benefits include:
- Cost-Effectiveness: CCA Copper Clad Aluminum wire is more affordable than pure copper wire due to the lower cost of aluminum. This makes it an economical option for large-scale projects.
- Weight Reduction: The use of an aluminum core significantly reduces the weight of the wire, which is advantageous in applications where weight is a critical factor, such as in the automotive and aerospace industries.
Common Applications
CCA wire is widely used in various industries due to its unique properties. Some common applications include:
- Electrical Wiring in Residential Construction: CCA wire is often used in residential buildings for electrical wiring due to its cost-effectiveness and adequate conductivity.
- Telecommunications and Data Cables: CCA Copper Clad Aluminum wire is utilized in telecommunications and data cables for signal transmission, providing a balance between performance and cost.